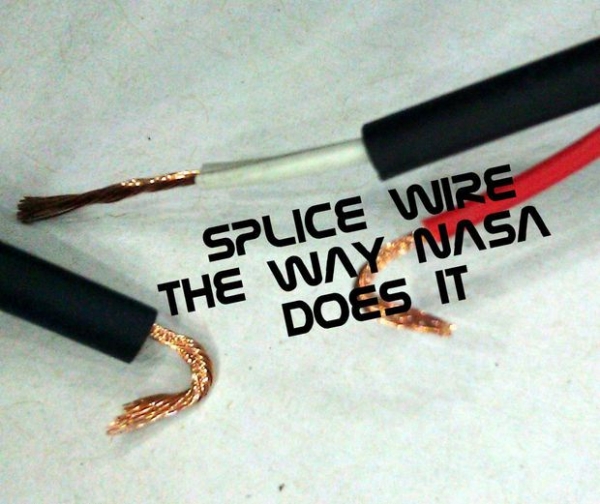
Often, in the world of electronic experimentation or repair, there’s a need to splice a wire or a 2-wire cable.
How many times have you seen a wire splice where the wires are sloppily twisted together and insulated with electrical tape, or worse, yet, masking tape?? A Plague Upon such slipshod methods! Don’t even go there. Such practices will only result in heartache down the road.
Do you want to make a strong, reliable, secure, neat connection in a 2-wire (or more) cable? This is not that hard. Despite the title, you don’t have to be a Rocket Scientist to make a neat wire splice and do it right.
The best splices are soldered, so knowing how to solder is essential in electronics.
The kind of splice we’re going to use is a modified Western Union or Lineman splice. Unlike ordinary twisted splices, this style has a very high tensile strength, which is why it’s the preferred method of NASA.
If it’s good enough for NASA, it’s definitely good enough for us!
Firstly here’s a video of the process
Step 1: Tools Needed
All you need to make a professional wire splice is:
- Wire cutters and strippers
- Needle-nose pliers
- A soldering iron and solder
- Heat-shrink tubing (Various sizes). You can get this at almost any store carrying electrical parts.
- Match, lighter, or heat gun to shrink tubing
- A few minutes of time
If you’ve done any kind of electrical or electronic work, you probably have all of these already.
Step 2: Prepare the wire ends


The important thing to do when splicing a multi-wire cable is to stagger the splices of the individual wires. This accomplishes two things: It reduces the possibility of a short circuit if your insulation method fails, and reduces the bulk of the splice so you don’t have a huge unsightly glob in the cable (also making it easier to thread the cable through holes if you need to).
Let’s get started. I’m using a laptop power cord as an example. If the cables you’re splicing have a jacket, gently strip about 1 1/2 inches of the jacket on each cable end, being careful not to nick the inner insulation. The wires here are color-coded, so we’ll be joining white to white, and red to red. On one cable end, cut one of the inner wires about 1/2″ shorter than the other. Strip 1/2″ from both wires. (These dimensions will vary depending on the thickness of the wires you’ll be joining. 1/2″ – 5/8″ works well for small gauge wires.)
Now, on the other end, cut 1/2″ off of the opposite wire – In other words, if you cut 1/2″ off of the red wire on the first end, cut 1/2″ off the white wire on the second end. Twist all the strands together tightly. When you are done, the wires should look like the second photo.
If splicing a cable containing more than two wires, stagger all the lengths by a similar amount. Of course, this will increase the total length of the splice.
The NASA method calls for the wires to be tinned (Coated with solder) before splicing. While this will probably improve the neatness of the splice, it makes the wire much stiffer and harder to bend and twist, so I did not do this on my demonstration project.
Step 3: Prepare Shrink Tubing
Heat-shrink tubing has got to be the greatest electronic invention since the transistor: Tight seal, conforms to irregular shapes, no gooey mess as one sometimes gets from tape, and more permanent than tape. If you want to make splices like a professional, this is what you want.
We are going to use two different sizes of heat shrink tubing: First, a small size to insulate the individual splices, then a larger size to cover and protect the whole repair. Choose shrink tubing the smallest diameter that will fit over your intended area, and somewhat longer than the splice. For the final jacket, I cut the tubing at least an inch longer than the total length of the spliced area. Put the large piece over the jacket and slide it several inches away from the splice area.
Put the short pieces over the longest individual wires; the object here is to get them as far away from the soldering as possible so they don’t shrink prematurely.
Step 4: Splice and Solder
Now we can splice. You did remember to slip your heat shrink tubing on already, didn’t you? This is the most common mistake that happens to everyone sooner or later… You just made a beautiful splice suitable for framing, and now you discover you left off the shrink tubing! Arrgh! So double-check you’ve got the tubing on first.
Bend each wire into a U shape and hook the mating wires together. Then twist both wires tightly around themselves, taking care not to leave any ends sticking out that could puncture the insulation.
Now solder the splice, working quickly to keep the heat away from the shrink tubing. Start the solder joint as far away from the tubing as you can. If you run into problems with the tubing shrinking prematurely, you can re-strip the wires to a slightly longer length, use a hemostat or locking tweezers as a heat sink between the soldering and the tubing, or try a wet rag as a heat sink.
Step 5: Insulate
Did your shrink tubing accidentally shrink? Dang it! You’ll have to re-do that connection. If it didn’t, though, you’re almost done.
Now slide the small shrink tubing over the solder joint so that it is roughly centered on the joint. Shrink it down with a match, lighter, or heat gun (Hair dryers may not get hot enough). Whatever heat source you use, keep it constantly moving – you can watch the tubing shrink and remove the heat as soon as it’s shrunk down. Don’t overheat the tubing – It can melt if you get carried away. Do this for all the wires you spliced.
Now slide the large piece of shrink tubing over the completed splice, overlapping the jacket ends on both sides. This will add some strength and durability to the whole assembly, so I like to make sure the shrink tubing overlaps the cable jacket by at least 1/2″ on both ends. Shrink this down, and bask in the knowledge that you made a professional, rocket-worthy cable splice!
Note: The splice shown in these photos obviously is not up to NASA standards, but it is using a modification of NASA’s approved method. The NASA document on splicing is 140 pages long, and, unless you’re building an aerospace vehicle, you don’t have to be as fussy. My splices are strong, reliable, and neat, and no one will die if they fail.
Via : Instuctables [Gizmologist]